World’s Longest Multi-Cutter Blade: 30 cm
I had a need for an extra-extra long multi-cutter blade, so we made one in Hal9k. Until proven otherwise, we hereby claim it to be the world’s longest, at about 30 cm from rotation point to the cutting edge.
Converting Starlock-MAX to Starlock-Plus
Initially I thought I could get away with just a 80mm long Bosch MAIZ 32 APB which seems to be the longest commercially available. First problem was that my multi-cutter was only “Starlock-Plus” and this blade is Starlock-MAX. Turns out, you can easily get around that: just drill up the hole to 10mm, and it fits like a glove, at least on the Starlock-Plus Bosch GOP 18V-28.
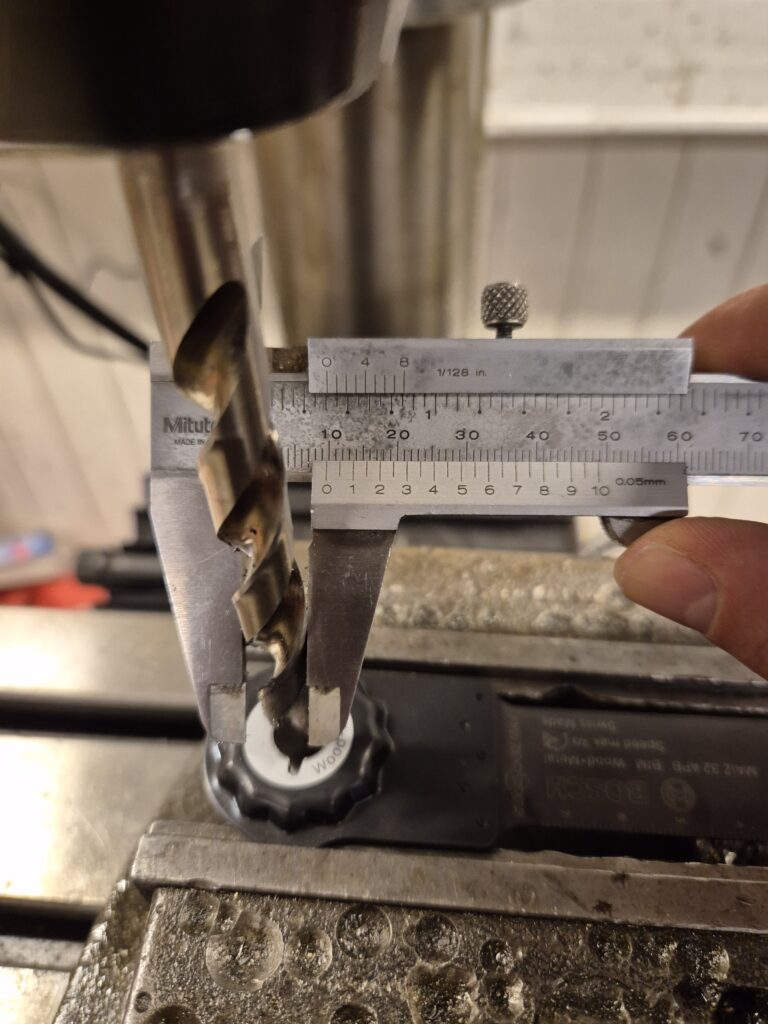
World record time
But as it turns out, I needed more length, and anything worth doing is worth overkilling! So sacrificing an old worn-out blade by welding on some 2mm steel plate provided a good base that would still attach to the multi-cutter.
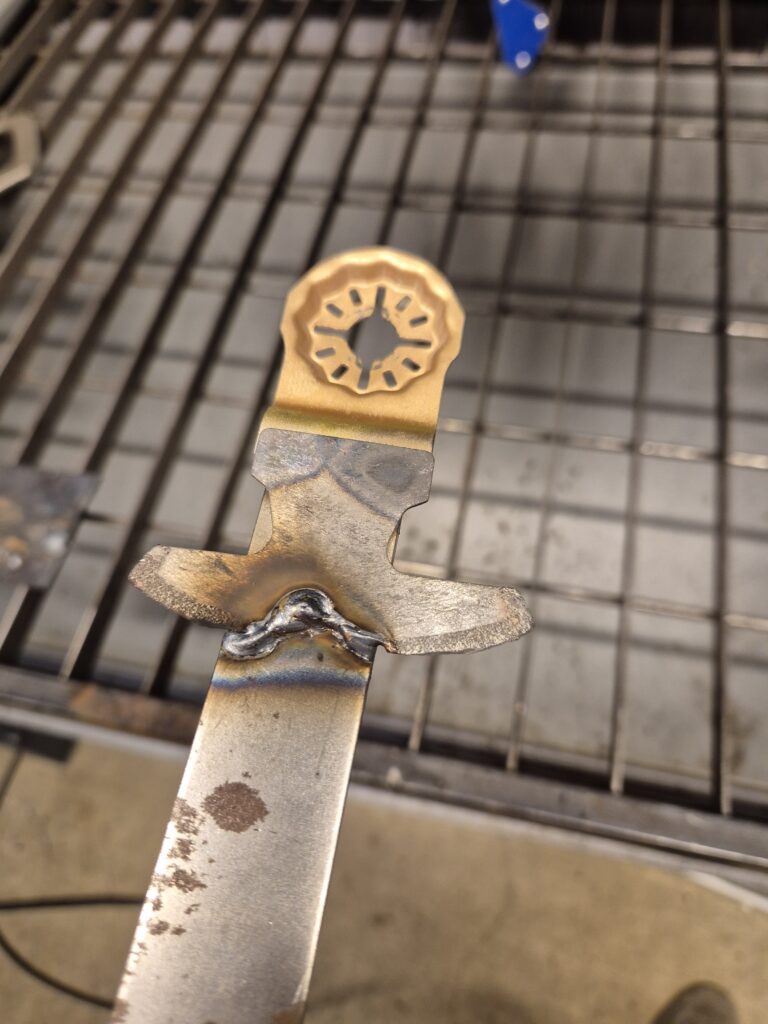
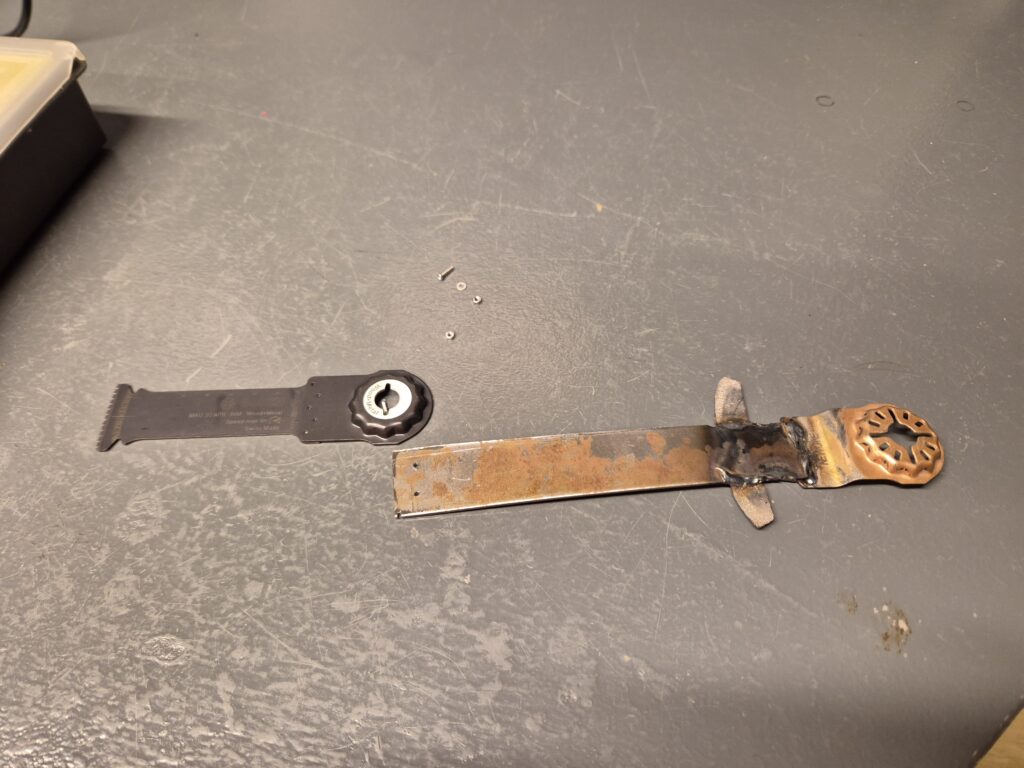
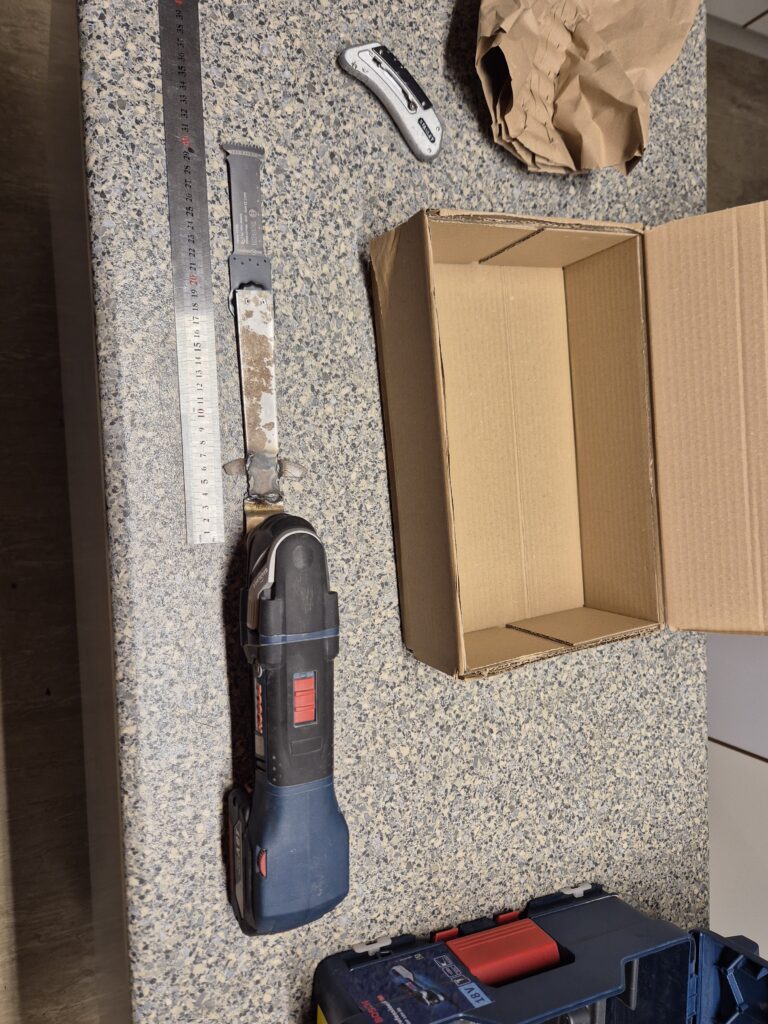
First attempt was just attaching the blade with two 2mm screws, as these are the largest that will fit in the star’s spikes and thereby prevent rotation. Initial testing:
So next solution was to beef up with a central 8mm bolt instead.
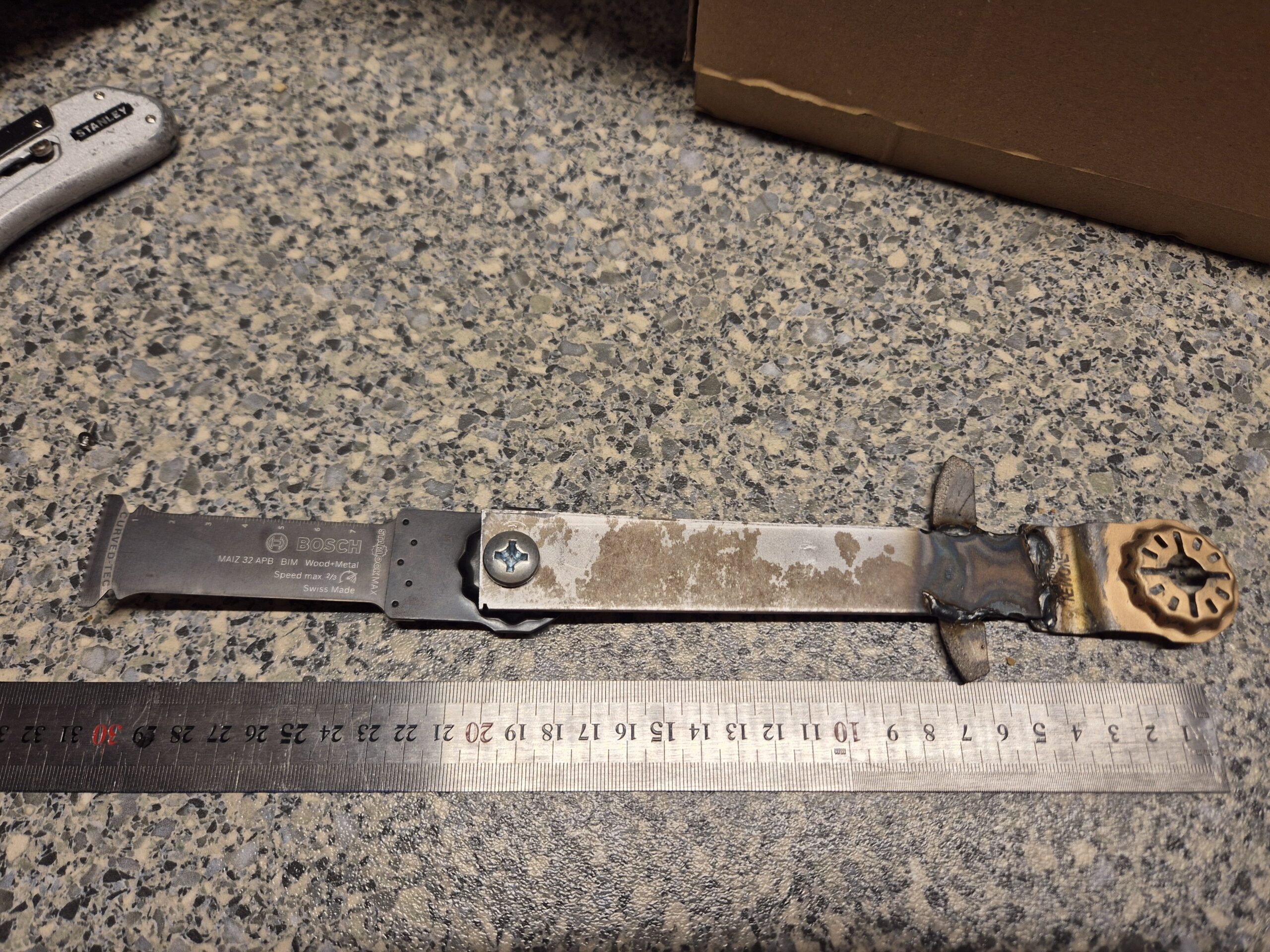
This worked much better if torqued enough (read: all you possibly can!), test-run went great after the initial oscillations:
And ultimately the cut in the tight corner was made, one-handedly in order to be able to film:
Great success!
This should not be considered safe, and several warranties were probably voided, but it got the job done.
Floating Solid Wood Alcove Shelves
I have an alcove where I wanted to put in some floating shelves. I wanted to use some solid wood I had lying around, to match the rest of the interior; this ruled out most of the methods described online: (i) building up the shelf around a bracket, and (ii) using hidden mounting hardware would be hard to get precise and would not provide support on the sides.
So inspired by some of the options instead I tried to get by with just brackets on the three sides, in a solid wood shelf. I ended up with 12mm brackets of plywood in a 26mm solid wood shelf, and that was plenty sturdy.
Step 1 was to cut out the rough shelves, with plenty of extra width, and rough fitting the plywood bracket pieces. It makes sense to leave as much on the top of the slit as possible, as this will be the failure point if overloaded. The excellent wood workshop at Hal9k came in very handy!
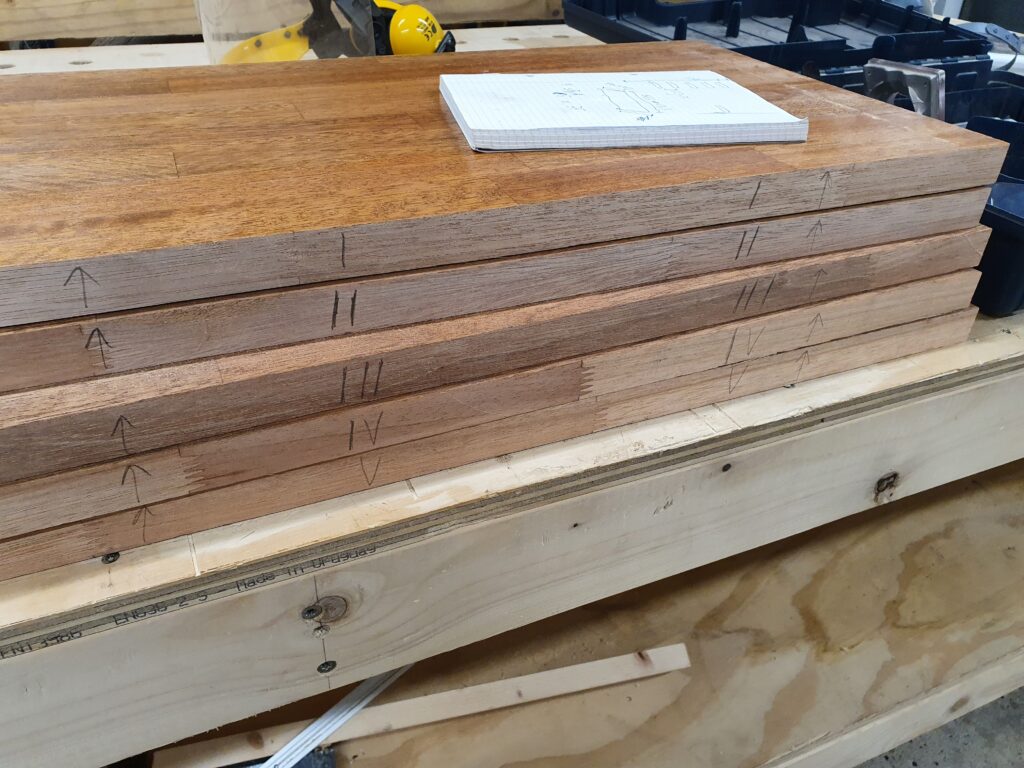

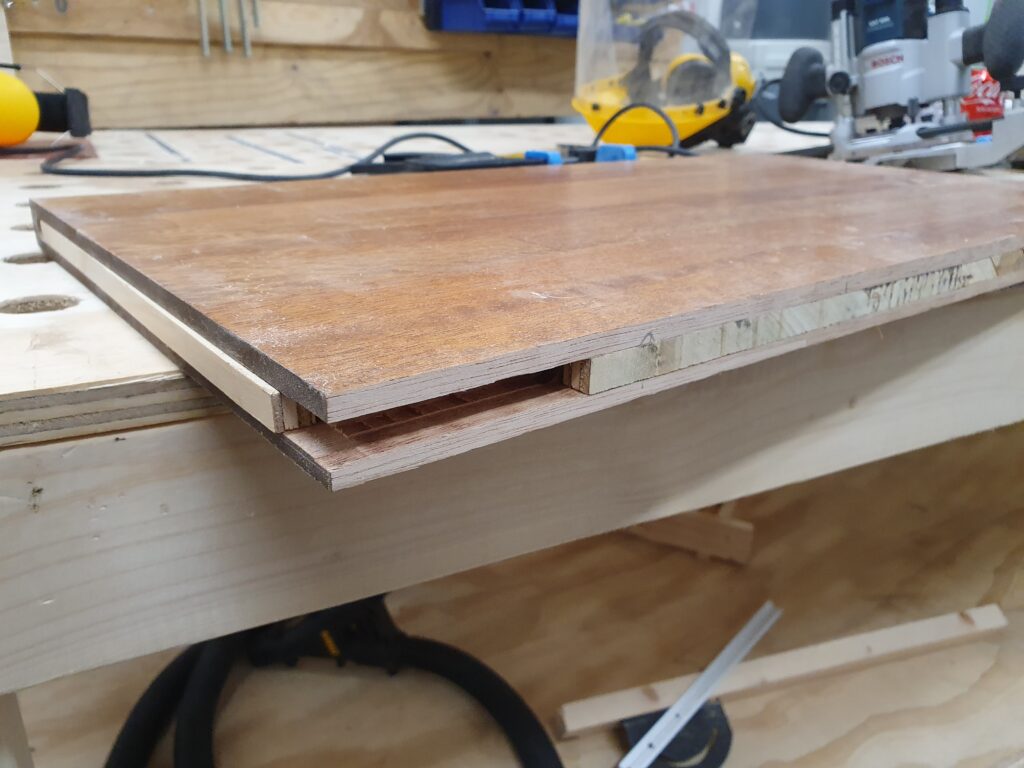
Step 2 was to mount the plywood brackets in the alcove. Pretty easy to do using a laser level, biggest problem was getting the rawplugs in precise enough for the level to be kept.
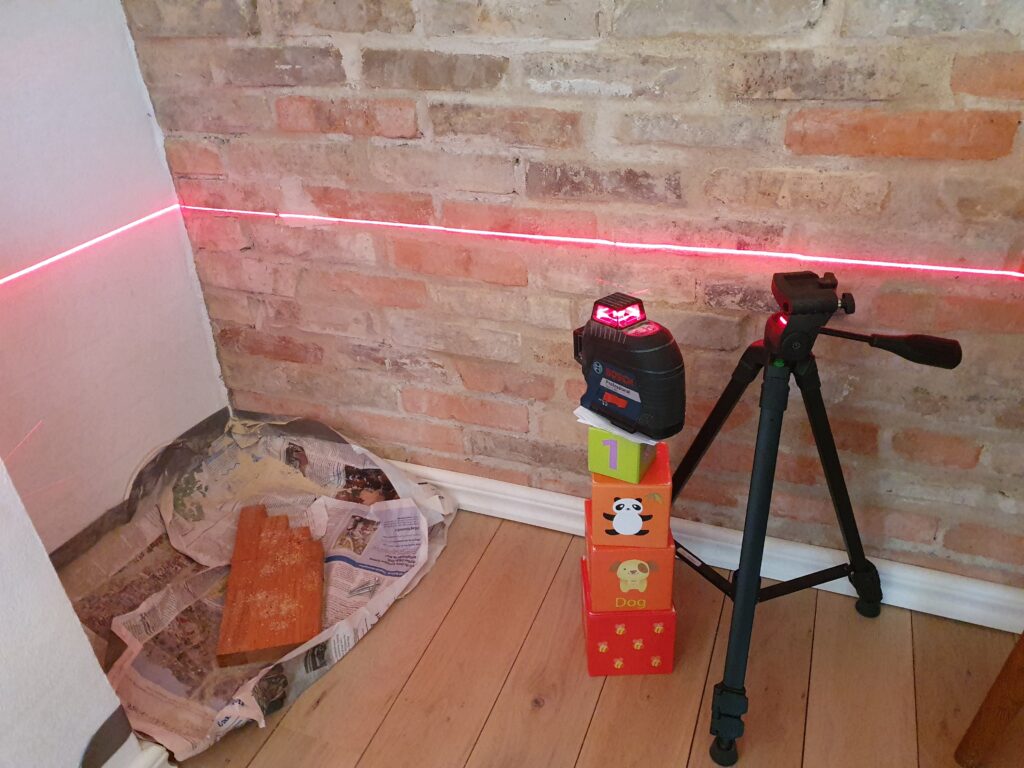
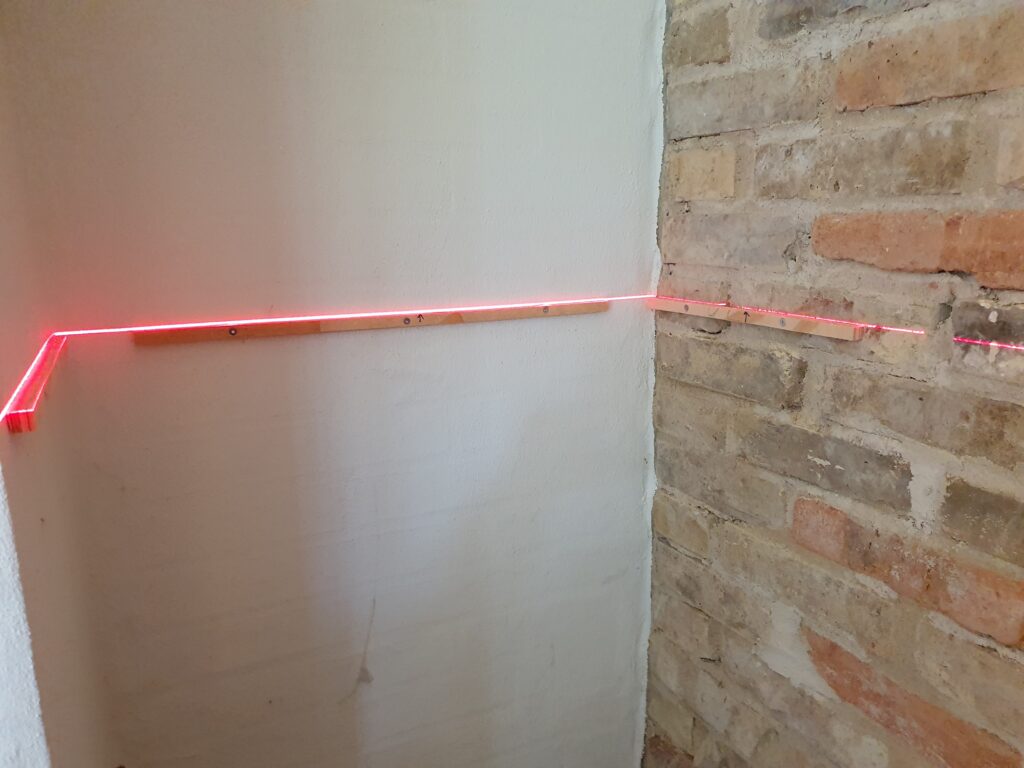
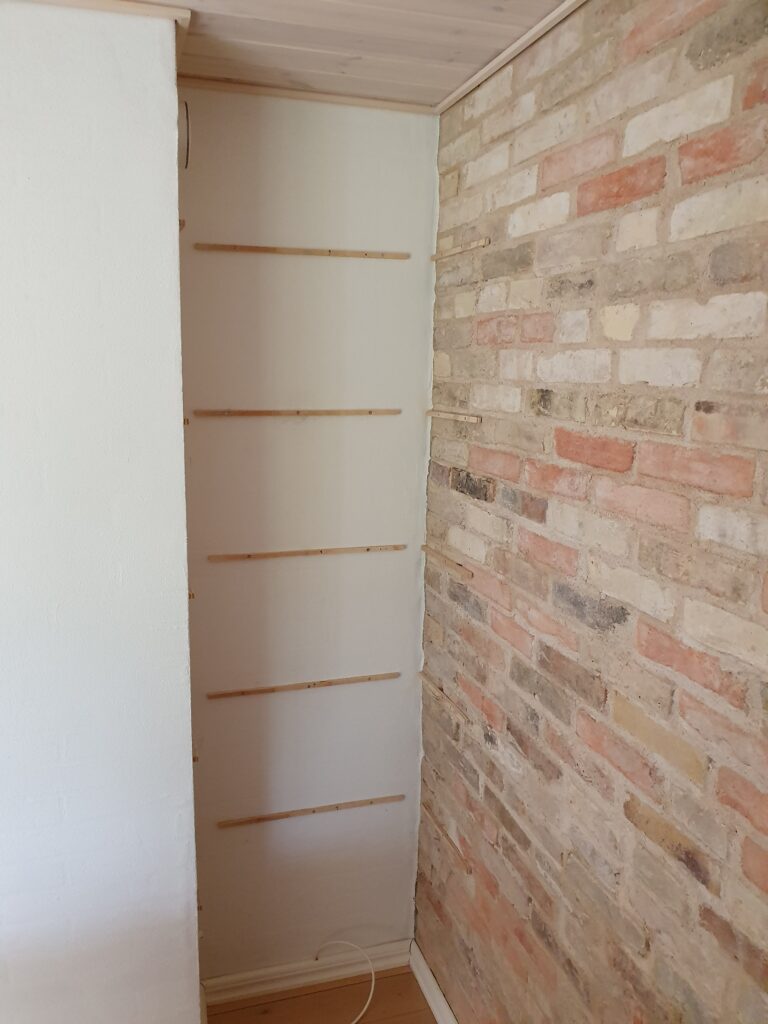
Step 3 was fitting the shelves individually, accounting for the crookedness of the 3 walls. The scribing method used by Rag’n’Bone Brown was pretty useful, just doing it in multiple steps to make sure not to cut off too much.
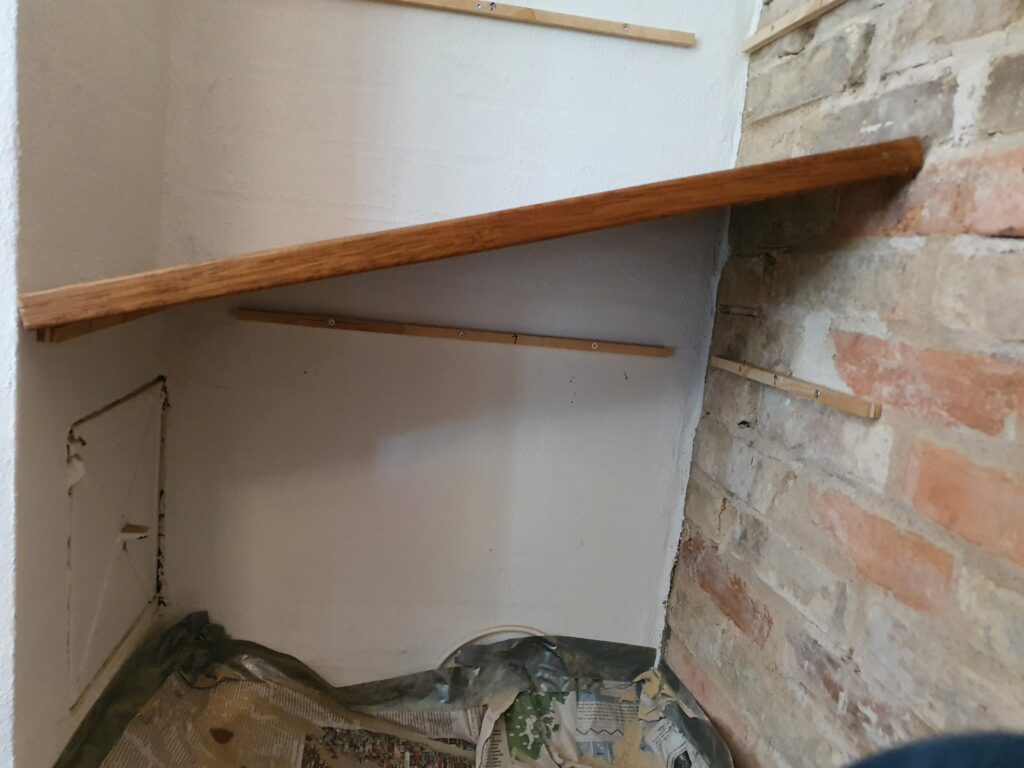
Finally, all the shelves in final mounting. Getting them in took a bit of persuasion with a hammer, and minor adjustments with a knife to the plywood brackets, as it was a tight fit. The key again was small adjustments.
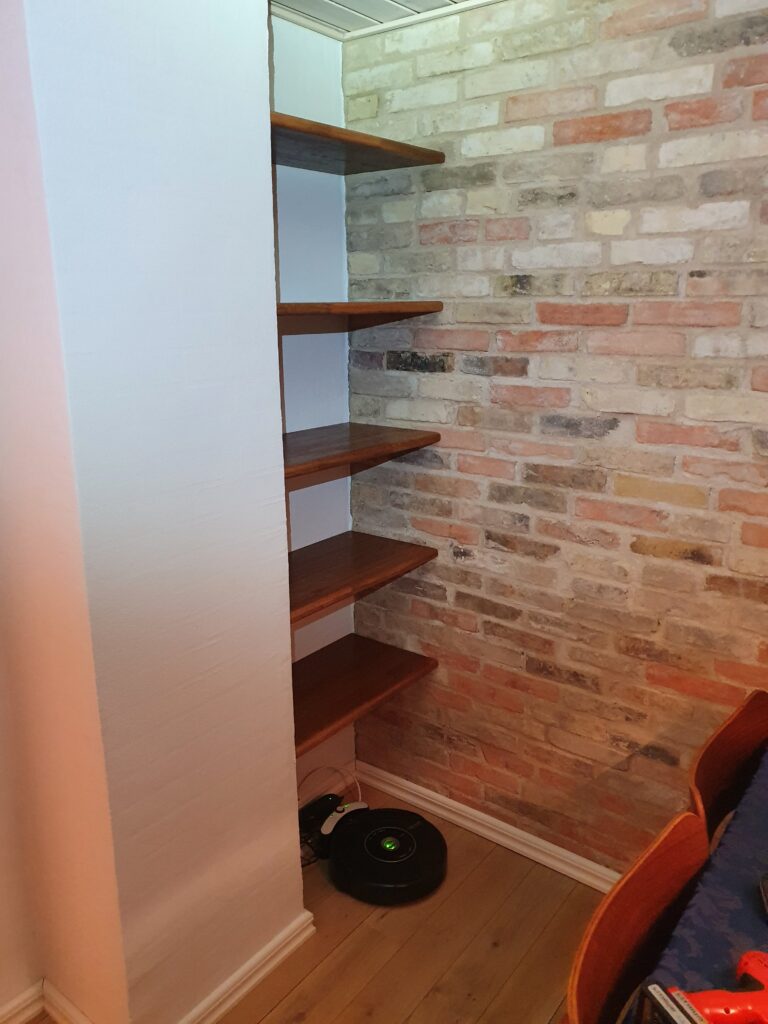
One concern with such a tight fit would be wood movement; however most of the wood movement is “across the grain” which in this application means “in and out” from the alcove, where the wood is basically free to move as the shelves are not fastened to the brackets in any way.
Another concern would be if the relatively small brackets (12x12mm) can handle the load of the relatively wide shelves (60cm wide, 35cm deep, and 2.6cm high). There are two failure scenarios: (i) the wood could split above the slit, (ii) or the bracket could deform or be pulled out. Neither seems likely as (i) applying a static (or even dynamic) load large enough to split the wood seems implausible, even at the weakest point in the middle of the front, and (ii) the tight fit counteracts the brackets ability to be pulled out since pulling out in one side would have the shelf hitting the wall on the opposite side.
All in all a very satisfying project to work on and complete!